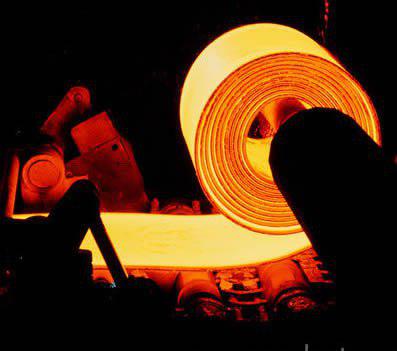
به گزارش
خبرگزاری صدا و سیما ؛ اردیبهشت ماه گذشته، مشعل های ریفورمر فولاد شادگان روشن شد و در فرایند راه اندازی گرم قرار گرفت. این کارخانه اولین طرح از طرح های فولاد استانی است که به روش تکنولوژی پرد (PERED) از روشهای نوین تولید فولاد ایجادشده است. این روش تولید آهن اسفنجی در 3 پروژه استانی دیگر نیز در دست اجراست.
پروژه های میانه ، نی ریز و بافت هم به ترتیب هر کدام بعد از اتمام پروژه اول، در مسیر تولید قرار خواهند گرفت، انتظار می رود در سال جاری، همه ی طرح های یاد شده به بهره برداری برسند. پرد (PERED) روش بهینه سازی شده برای تولید آهن اسفنجی است.
این تکنولوژی با عنوانPersian Reduction، در آلمان و تحت لیسانس شرکت ایرانی MME به ثبت رسیده است. به گفته کارشناسان و متخصصان صنعت فولاد بهره گیری از این روش جدید برای تولید آهن اسفنجی نسبت به روش های سابق مزیت هایی را به دنبال دارد. با دستیابی به این تکنولوژی در جهان صنعت فولاد ایران، مسیر کاملا متفاوتی را در زمینه تولید دنبال می کند .
کارشناسان با توجه به اهمیت این تکنولوژی ایمیدرو در میزگردی ، به بررسی « تکنولوژی بومی تولید آهن اسفنجی PERED » نسبت به سایر تکنولوژی های روز جهان همچون MIDREX و HYL و ... پرداختند و معتقدند تکنولوژی ِپرِد نقطه عطف صنعت فولاد کشور است و تحول این صنعت را درپی خواهد داشت.
متخصصان این میزگزد بر این نکته تاکید داشتند که دستیابی به دانش و تکنووژی پِرِد حاصل اعتماد مدیران به شرکت های داخلی، خودباوری و ریسک پذیری مدیران ارشد بخش صنعت و معدن بوده است.
اسدالله فرشاد مدیرعامل فولاد غدیر ایرانیان و مولف کتاب تکنولوژی آهن اسفنجی، محمد رحیم رستی مدیرعامل هلدینگ توسعه فولاد جنوب و از مدیران باتجربه صنعت فولاد، حسن کرباسچی مدیر دفتر MME در تهران (شرکت صاحب تکنولوژی ایرانی تولید آهن اسفنجی (Persian Reduction) و حسین عزیزطائمه مدیر بخش مهندسی MME در این میزگرد به بررسی این تکنولوژی مذکور از زوایای مختلف پرداختند.
رستی گفت : تکنولوژی بومی PERED با مشورت گروهی از کارشناسان هندی و آلمانی روی آهن اسفنجی و فولاد سازی به سرانجام رسید.
وی افزود : کشور ما بیشترین میزان تولید آهن اسفنجی در جهان با استفاده از گاز را دارد . ایران از نظر منابع انرژی و گاز طبیعی دومین کشور در دنیا است و به همین خاطر توسعه فولاد متکی بر گاز طبیعی خواهد بود. از نظر تجربه تولید، از دیگر کشورها جلوتر هستیم . برخی متخصصان ایرانی در خارج روی اینگونه تکنولوژی ها کار کردند و متاسفانه دستاوردهایی که ایرانی ها در آن نقش داشتند به نام آن کشورها ثبت شد. اما فولادسازی با متفرق شدن تیم ایمیدرو و شرکت ملی فولاد عملا مثل احیاء ادامه پیدا نکرد. این اتفاق وقتی روی داد که ریسک کردن کار سختی بود. معتقدم تیم منسجم در ایمیدرو، شرکت فولاد و MME این شهامت را به خرج دادند و این ریسک را پذیرفتند که این تکنولوژی در چهار واحد فولادسازی اجرا و پیاده سازی شود. تکنولوژی که – در آن زمان- حتی یک واحدش نصب و اجرا نشده بود.
فرشاد هم اظهار داشت : در عرصه توانمندی های ساخت، سازندگان داخل کشور و پیمانکاران بزرگ در قالب سمینارها و نمایشگاه های سالانه، توانمندی های خود را عرضه می کنند. آنچه که مهم است بحث توانمندی های مهندسی است. از همین رو "ایریتک" به عنوان پیشانی مهندسی ایران شکل گرفت و با حمایت های شرکت ملی فولاد در آن مقطع که بحث احداث کارخانه مبارکه مطرح بود با مجموعه تِنُوا و جِنُوا و شرکت ایریتک شکل گرفت. این مجموعه با فضا و امکاناتی که برایش در فولاد خوزستان مهیا شد میدرکس 600 (هزارتنی) را توسعه داد و اولین مدول 800 هزارتنی زمزم در فولاد خوزستان را راه اندازی کرد. بعد از آن به اتکای این حرکت و حمایت هایی که صنعت فولاد از جمله شرکت MME و MMTE از مهندسان داخل انجام داد، توسعه ظرفیت احداث ظرفیت آهن اسفنجی و کارخانجات احیای مستقیم با روشی متفاوت تر از میدرکس شکل گرفت. بعدها در آلمان گروه متخصصی بین سالهای 75 تا 80 میلادی وقتی مجموعه مانیسمان، اس ام اس و مان جی اچ اچ طراحی کوره های EBT (تخلیه از کف) کار کردند شرکتی به اسم فوکس قصد داشت حق لیسانس این تکنولوژی را نپردازد. بنابراین شرکت های ایرانی به دنبال این بودند که کار متفاوتی انجام دهند تا از پرداخت هزینه های اضافی از جمله حق عضویت و لیسانس جلوگیری کنند.
وی افزود : وقتی تکنولوژیی ایجاد می شود و می خواهد دستاوردهایش را به جامعه جهانی معرفی کند نیاز به یک رفرنس معتبر دارد. اگر تولید فولاد به روش احیای مستقیم، بومی سازی نمی شد ما باید برای هر مدول میدرکس دقیقا دو برابر این سرمایه گذاری را توسط خارجی ها انجام می دادیم.
فرشاد گفت : دومین واحد که از این تکنولوژی بهره می برد فولاد نی ریز است و تا مهرماه امسال دومین مدول پِرِد به بهره برداری می رسد.
دلیل اینکه چرا به این نوع تکنولوژی که به دست متخصصان ایرانی ساخته شده می بالیم این است که ایران تولید بیش از 50 درصد آهن اسفنجی جهان را به خود اختصاص داده است و در آینده با توجه به چشم انداز 55 میلیون تنی، بهرمندی از چنین دستاوردهایی فعالیت هایمان را تسهیل خواهد کرد. توجه داشته باشیم که بیش از 35درصد از کل فولاد دنیا با روش کوره های قوس الکتریک تولید می شود که خوراک مناسبش آهن اسفنجی است. فکر می کنم در این زمینه رسالتی بر دوش شرکت های ایریتک، MME و MMT است. MME توجه ویژه بر روی پرفورمنس پلنت باید داشته باشد. این روش با میدرکس مشابهت ها و تفاوت هایی دارد.
فرشاد گفت : از مزیت های اساسی این روش می توان به میزان سرمایه گذاری پایین تر، هزینه های بهره برداری کمتر، آلودگی کمتر زیست محیطی، قابلیت انعطاف برای مصرف سنگ آهن و همچنین امکان دستیابی به ظرفیت های بیش از یک میلیون تن در سال اشاره کرد.
کرباسچی هم در این میزگرد گفت : متخصصان ایرانی بر اساس تجارب خود، ابتدا یک ایده را مطرح و سپس روش احیای جدیدی را تحت عنوان PERED ابداع کردند. در این تکنولوژی تلاش شده تا از مزایای دو روش قبلی بهره گرفته شود و حتی در موارد متعددی این قابلیتها افزایش پیدا کند. در تکنولوژی نام برده، امکان تولید محصولات متنوعی همچون احیای مستقیم سنگ آهن، Direct Reduced Iron ، بریکت گرم آهن اسفنجی (HBI) و HDRI مطابق با نیاز مشتری وجود دارد. برای تولید محصولات در تکنولوژی یاد شده میتوان از گاز طبیعی یا گاز سنتز استفاده کرد. لازم به ذکر است که واحدهای احداث شده با این تکنولوژی هر ساله با ظرفیت حدودی 800 هزار تن میتوانند تا حدود یک میلیون تن آهن اسفنجی تولید کنند.
وی افزود : به لحاظ وجود منابع سرشار گاز طبیعی به عنوان مواد اولیه در ایران در پروسه فولاد سازی استفاده از آهن اسفنجی، استفاده از تکنولوژی پرد در کشور ما ضروری بود. تولید آزمایشی آهن اسفنجی با تکنولوژی پرد 1ماه پیش با ریت ( نرخ ) خوب شروع شد و خوشبختانه به موفقیت هایی دست پیدا کردیم و در ادامه برای این تکنولوژی اصلاحاتی برایش در نظر گرفتیم. بحث اینکه چه شد که سراغ این تکنولوژی رفتیم، این بود که متخصصان به این جمع بندی رسیدند فعالیت های انجام شده در ایران و چه در خارج روی تکنولوژی های تولید آهن اسفنجی ارزیابی شود.
سال های گذشته در راستای اهداف اقتصاد مقاومتی و عدم وابستگی نسبت به تکنولوژی که به هرحال حق لایسنس باید پرداخت می کردیم؛ خارجی ها یک سری اصلاحات این تکنولوژی را به دلیل تحریم ها به ما نمی دادند و محدودیت هایی را ایجاد کردند. این ایده از اوایل دهه 1380 مطرح و در سال 86 قراداد آن امضا شد. در این راستا MME به عنوان تنها شرکت فنی مهندسی ایمیدرو عهده دار ساخت این تکنولوژی شد و جمعی از متخصصان ایرانی به اضافه متخصصان عمدتا هندی، این تکنولوژِی را به نام کشورمان به ثبت رساندیم و در چهار پروژه استانی شادگان بافت، نی ریز و میانه از آن استفاده خواهد شد. در راه اندازی این تکنولوژی نگرانی هایی نه در سطح فنی بلکه در سطح مسئولان کلان وجود داشت که خوشبختانه در اولین گام توانستیم آهن اسفنجی با مزایایی برتر تولید کنیم. یکی از ویژگی های پرد این است که در 24 ساعت اول توانستیم به متالیزاسیون 93 درصد برسیم و میزان تولید نزدیک 70 تن در ساعت دستاورد بزرگی بود. چیزی که در تکنولوژی مشابه دیده نشده است.
کرباسچی گفت : چون تکنولوژی جدیدی بود انتظار می رفت که در بعضی تجهیزات مشکل ایجاد شود و انتظار می رفت یک هفته تا رسیدن به محصول طول بکشد. اما به رغم زمان های تولید محصول در فرایندهای مشابه این خودش دستاوردی بود که به نوعی همه را شوکه کرد. این تکنولوژی آنقدر دقیق طراحی شد که توانسته با این محدودیت ها یک تولید خوب با کیفیت با نرخ تولید بالا عملیاتی شود. طی روزهای گذشته 82 تن در ساعت افزایش پیدا کرد. اواخر هفته و 10روز آینده به تولید 100 تن خواهیم رسید.
در ادامه اقای فرشاد گفت : زمانی که می خواهیم یک تکنولوژی را به ثبت برسانیم باید مراقب باشیم که کپی برداری دقیق از میدرکس نباشد. وقتی مدول زمزم با ظرفیت 800 هزارتن احداث شد کار مهندسی اش در ایران انجام گرفت؛ شرکت کوبه که لیسانس آن را از میدرکس خریداری کرده بود، اقدام به Claim ( ادعای حقوقی) کرد و باعث شد که با تحت فشار گذاشتن ایریتک و ام ام تی، با کوبه (استیل) قرارداد ببندند که "کانسترکشن فی" (رقم پولی بابت ساخت) و هم لایسنس فی ( رقم پولی بابت اعطای مجوز) را به کوبه بدهند.
اکنون هم مگامدول هایی که در ایران زدیم، با پیگیری های مستمر موفق شد هم لایسنس فی را و هم کانسترکشن فی را برای اپریشن (بهره برداری) بگیرد. شکی در این نیست که وقتی می خواهیم طراحی ایرانی را ثبت کنیم، باید از جهاتی تفاوت های اساسی با میدرکس داشته باشد.
کوبه ژاپن خواهان همکاری شد
کرباسچی هم گفت : وقتی در کشور برنامه های زیادی برای تولید آهن اسفنجی داریم بنابراین به دنبال این رفتیم که تکنولوژی آن هم در اختیار خودمان باشد. این انتظار نیز هست با توجه به نتایج بدست آمده، این تکنولوژی را صادر کنیم. در این زمینهMME پروژه مشترکی را به نام CSTM با چینی ها به میزان 300 هزار تن دارد. چون تا به حال ریفرنس نبود مقداری هم این اعتماد در آن زمان کم شد الان بعد از پروژه شادگان که تولید آزمایشی آن را داریم ظرف یک ماه تا دوماه آینده در میانه و نی ریز دومین و سومین کارخانه پرد به تولید آزمایشی می رسد. در حال حاضر همه توجه ها به این تکنولوژی است و از کوبه ژاپن با مجموعه ما تماس گرفته شد و درخواست همکاری دادند!
"کوبه" : نمی توانید!
در ادامه اقای رستی اظهار داشت : اگر ما این تکنولوژی را نداشتیم حتی طرح های میدرکسی را که نصب کردیم به ما در شرایط تحریم اجازه تولید نمی دادند. در گذشته، شرکت های کوبه و میدرکس برای واحد زمزم در خوزستان به هیچ وجه با ما همکاری نمی کردند و فقط برای بازدید به ایران سفر می کردند و اذعان می داشتند شما هیچ وقت نمی توانید آن را به بهره برداری برسانید! جالب اینکه وقتی این مجموعه به بهره برداری رسید آمدند گفتند این را به اسم میدرکس ثبت کنید و به اسم زمزم نباشد!
در ادامه اقای فرشاد افزود : فعالیت در عرصه صنعت آهن و فولاد، طی 5دهه که شروع آن در اهواز و اصفهان بود، پایه ریزی شد. باید گام های بلندتری برمی داشتیم. ما در بحث های دیگر هم جای کار داریم. اما مهم بحث اقتصادی موضوع است. پرد برای اقتصادی کردن توسعه صنعت است. تولید آهن اسفنجی می تواند گام هایی را بردارد که فردا رقابت را بر ایرتیک و هم MMTE افزایش دهد. هر گامی که MME بر می دارد به ارتقای توان مهندسی ایران کمک خواهد کرد.
این تکنولوژی به چه میزان در کاهش هزینه ها اثر گذار است؟
در این باره اقای کرباسچی گفت : در عمل باید راستی آزمایی شود که این مواردی که شرکت MME بر اساس محاسباتش و بر اساس تکنولوژی که آن مزایا و کاهش مصارف را ایجاد می کند؛ تا چه اندازه عملی می شود. یعنی بعد از اینکه به ظرفیت اسمی رسید به صورت دوره ای باید خروجی آن رصد شود و مصارف حامل های انرژی با روش های مشابه دیگر را مقایسه کنیم. با توجه به نتایج مثبت در تولید آزمایشی به نظر می رسد بهبودهایی که در
میزان تولید به وجود آمده کاهش مصارف را نیز یه همراه خواهد داشت.
عزیز طایمه هم ادامه داد : هدف از طرح پرد کاهش مصارف و توسعه تکنولوژی است و شعار ما این است که بر روی لبه تکنولوژی هستیم. طرح پرد شاهکار احیای مستقیم است و خروجی این شاهکار قیمت تمام شده خواهد بود. یکی از مزایای این طرح کاهش مصارف است. بخشی از کاهش مصارف به پاک بودن این تکنولوژی و بخش دیگر به ساختار بر می گردد.
رستی گفت : اگر این تکنولوژی را نداشتیم و اگر می خواستیم طرف های خارجی کارخانه های احیای مستقیم بسازند، تا دوبرابر از ما پول می گرفتند.
یکی از مزیت های محصولات پرد این است که حمل و نقل آهن اسفنجی آسان می شود. (چراکه به علت ترکیب با اکسیژن، اکسید می شود) تولید با تکنولوژی پرد عمل اکسید شدن را کاهش می دهد. از سوی دیگر نقدی که به این تکنولوژی وارد شده، این است که وقتی خروجی اجرای این طرح مشخص نشده چرا در یک بازه زمانی فشرده باید در 4 مجموعه فولادی مورد استفاده قرار بگیرد.
در ادامه کرباسچی اظهار داشت : در حال حاضر شرکت MME در جهان شناخته شده و قطعا در زنجیره فولاد در قدم بعد و در بالادست، از کنسانتره و گندله و در پایین دست توسعه بازار خواهیم داشت ، همچنین در صنایع غیر فولادی مثل سرب و روی نیز برنامه خواهیم داشت.
ما همین کاری که در تکنولوژی پرد انجام دادیم وظیفه داریم در تکنولوژی های دیگر به دانش فنی دست پیدا کنیم. ایمیدر و دیگر شرکت ها یکسری نیازهایی در صنعت معدن و صنایع معدنی دارند و ما به دنبال این هستیم که با توجه به امکانات موجود برای انتقال دانش فنی به عنوان یک پل ارتباطی از اروپا به ایران باشیم.
جزو 5 کشوری صاحب تکنولوژی آهن اسفنجی هستیم
عزیز طایمه در این باره گفت : ایران جزو 5 کشوری است که اجازه ساخت چنین تکنولوژی را دارد . میدرکس اجازه ساخت یک واحد به هیچ وجه نمی دهد و پرد برای اجرا در هر کشوری کاملا مستقل است ما می توانیم مجوز یا لاینسنس بفروشیم. به عنوان مثال ما برای شرکتی در برزیل می توانیم لاینس ساخت پرد ارایه کنیم و اجازه ساخت این تکنولوژی را به هرمجموعه خارجی بدهیم.
کرباسچی هم گفت : در داخل یکی از مزیت های ما این است که قطعا در حد و اندازه قابل ملاحظه و مزیت رقابتی، (نسبت به روش های مشابه) پروژه اجرا می کنیم.
رستی در این باره اظهار داشت: وقتی MME وارد ایران شد و خواست این پروژه را اجرا کند در مناقصه شرکت کرد و رقبایش تکنولوژی های "میدرکس" و "اچ وای ال" بودند. در کنار آن ها در این مناقصه حضور یافت و 4 طرح از 8 طرح را برنده شد و این در حالی است که تنها امتیازی که به ما داده بودند این بود در سال 86 می توانستیم در این مناقصه شرکت کنیم.
در ادامه اقای فرشاد تاکید کرد : برغم اینکه در آن سال ها این طرح رفرنس نداشت مدیران این ریسک را پذیرفتند ما در دوره ای که تحریم ها برداشته نشده بود به جامعه جوان مهندسی میدان دادیم. در پامیدکو، با هدف بومی سازی تولید گندله، این حرکت صورت گرفت. در ایران فولاد آلیاژی تولید نمی شد و با قیمت های دوبرابر امروز واردات داشتیم. ما اگر به مجموعه همچون MME میدان ندهیم نمی تواند توسعه بازار داشته باشد. جمعی از مسئولان جرات و جسارت پیدا کردند این قرارداد را امضا و در مناقصه با قیمت مناسب تر شرکت کردند. مطلب بعدی در تهیه کاتالیست است. الان دو شرکت سرو و خوارزم را داریم که کاتالیست تولید می کند و پیش از این کشور دیگری با هر قیمت دیگری به ما عرضه می کرد. در این زمینه امروز در تولید کاتالیست به جایی رسیدیم که تولیدکنندگان ما اعلام کنند ما تعهد می دهیم برای شرکت معدنی سیرجان اگر کاتالیست های تولیدی جواب نداد تا 5 سال رایگان کاتالیست در اختیار این کارخانه قرار می دهیم و همچنین ضرر و زیان هم پرداخت می شود.
کرباسچی: هنوز یکی از کاتالیست های واحدهای ما در فولاد بافت خریداری نشده است. با توافقات صورت گرفته قرار شد این نوع قطعه از شرکت های داخلی خریداری شود. به نظر من در بحث استفاده از دانش ایرانی باید ریسک کرده و انتظارات خود را تعدیل کنیم. برخی مسئولان به متخصصان ایرانی میدان دادند و نتایج این اعتماد را نظاره گر بوده اند. اگر مقداری از نتایج ضعیف بود باز باید حمایت شود. بنابراین انتظار ما این است بر روی تکنولوژی پرد چنین سیاستی از جانب دست اندرکاران و مجموعه ایمیدرو و وزارتخانه به کار گرفته شود.
بنابراین گزارش اقای رستی هم گفت : این تکنولوژی بدون اینکه راه را برای تکنولوژی های دیگر ببندد طراحی شده است و می تواند رشد کند و به حیات خود ادامه دهد.
عزیز طایمه هم اظهار داشت : اولین کارخانه ای که در ایران، توانست روز اول 93 درصد متالیزاسیون (تبدیل به فلز) بگیرد پرد بود. برخی اوقات دو ماه طول می کشید تا به متالیزاسیون مورد نظرمان برسیم. در مورد تغییراتی که به واسطه استفاده از این تکنولوژی در کوره های جدید به وجود آمده باید گفت در روشهای معمول تولید آهن اسفنجی، گاز احیایی از طریق یک داکت به کوره وارد میشود. اما در تکنولوژی جدید، ورود این گاز با استفاده از دو داکت مجزا، انجام میشود. بنابراین از یک سو یکنواختی و هموژنی گاز احیایی را افزایش میدهد و از سوی دیگر میتوان کنترل آن را بیشتر از روشهای قبل در اختیار داشت.
وی گفت : در روشهای قدیمی تولید آهن اسفنجی، 3 کلوخه شکن بالایی، میانی و پایینی استفاده میشود؛ در حالی که در روش PERED، یکی از کلوخه شکنها حذف شدهاند. همچنین در روشهای معمول، گندله بهصورت اختاپوسی به کوره تزریق میشد. اما در طرح جدید PERED، لوله تغذیه دیگری برای ورود گندله در مرکز کوره نیز تعبیه شده است. این امر موجبات یکنواختی و تامین یکنواخت خوراک را فراهم میکند و در نهایت کارایی را افزایش خواهد داد. همین موضوع نیز، میتواند یکی از عواملی باشد که زمینه را برای حذف یکی از کلوخهشکنها، مهیا کند.
در روش MIDREX از لولههایی با قطر 8 اینچ بهعنوان ریفورمر استفاده میشود. اما در طرح جدید برای پلنت های 800 هزار تنی، این قطر تا 10 اینچ افزایش یافته است که موجبات کاهش تعداد لولهها را فراهم میکند و اندازه نهایی محفظه ریفورمر هم کوچک تر میشود. در روش جدید از کاتالیست منحصر بهفردی استفاده میشود. این کاتالیست، شکست گازهای احیایی را تسریع میکند و طول عمر بیشتری نیز دارد. لازم به ذکر است که واحدهایMIDREX به کمپرسورهای ارزان تر مجهز هستند. در حالی که در طرح جدید از کمپرسورهای سانتریفیوژی زیمنس استفاده میشود.
این جایگزینی، آزادی عمل بیشتری را ایجاد می کند و هزینههای مصارف برق و ... و نیز سرمایه گذاری را کاهش میدهد. در طرح جدید تولید آهن اسفنجی برای پلنت های 800 هزار تنی، رکوپراتور (سیستم بازیاب حرارتی) بهصورت معکوس نصب شده است.
همچنین در کورههای MIDREX خنک کردن کوره بهصورت نقطهای و سپس درخت کریسمس انجام میشود. اما در روش PERED، خنککنندگی از طریق خط محیطی انجام میشود. بنابراین خنککاری در روش جدید از توزیع، اثرگذاری و کارایی بیشتری برخوردار است.
تمامی موارد یاد شده در نهایت موجبات بهبود فرآیند احیا را در این ابداع جدید فراهم میآورند.
در واقع باید گفت که تغییرات ایجاد شده مزیتهایی را بهدنبال دارند. کاهش میزان سرمایهگذاری اولیه یکی از مهمترین مزیتهای روش PERED بهشمار میرود؛ همچنین نباید از توجه به این نکته غافل بود که سرمایه مصرف شده نیز در داخل کشور استفاده خواهد شد و موجبات رونق هر چه بیشتر صنایع داخلی را فراهم میآورد. بنابراین نباید از این نکته غافل بود که دوره زمانی راهاندازی و رسیدن به محصول در اینگونه طرحهای جدید، از یکسو به علت تازگی تکنولوژی و از سوی دیگر بهدلیل برخی مشکلات یاد شده برای تجهیزات، طولانیتر از زمان های متداول در راهاندازی واحدهای میدرکس خواهد بود.
تکنولوژیهای میدرکسی که در گذشته احداث شدهاند را میتوان تا حدودی و نه صد درصد، بهبود بخشید و به PERED تبدیل کرد.
این طرح برای فولاد خوزستان انجام شد و طی آن، ظرفیت 650 هزار تنی این واحد به 850 هزار تن ارتقا یافت، یعنی با این تغییرات 30 درصد افزایش ظرفیت ایجاد شد.